Da empleo a casi 5.000 personas de forma directa y a más del doble de forma indirecta. La planta de Volkswagen Navarra lleva fabricando turismos para la marca alemana desde 1984 cuando inició la producción del Polo, modelo que desde entonces se ha mantenido de forma ininterrumpida en sus cadenas de montaje y al que acababa de unirse un tercer modelo, el Taigo, tras la llegada el año pasado del T-Cross.
Pero la historia de esta emblemática planta navarra viene de mucho más atrás, no en vano en sus primeros años de vida la entonces fábrica española de Automóviles de Turismo Hispano-Ingleses (AUTHI) produjo entre 1968 y 1975, ya en el polígono Landaben de Pamplona, nada menos que dos modelos de la marcas Austin y Morris bajo licencia, siendo probablemente su modelo más emblemático entonces el popular Mini 1275C a los que siguió en 1969 dos modelos más, el Mini 1000 Estándar y Especial.
La crisis económica que sufrió a mediados de los años ’70 terminó por cerrar sus puertas reabiertas tiempo después a manos de Seat, fabricando allí modelos con licencia Fiat como el 124 y el Panda –incluso modelos de Lancia– hasta que tras romper los acuerdos con la italiana cambió de socio a Volkswagen y comenzó en 1984 la producción del Polo, el modelo más producido en la planta ubicada en Landaben.
Desde entonces ha producido de forma exclusiva este modelo que le sirvió para convertirse en una de las fábricas más eficientes del grupo en Europa que le ha valido para ampliar su cartera de modelos primero al T-Cross en 2020 y, ahora, al nuevo Taigo.
Y con ocasión de su lanzamiento hemos podido visitar esta emblemática planta navarra, un pilar en la economía de la región, y descubrir algunos de sus secretos que le han valido situarse como una de las mejores fábricas por productividad de las más de 30 que la multinacional tiene en Europa.
La gestión logística, una referencia en Europa
Y aunque en la línea de montaje tiene su parte más atractiva por la eficiente gestión que le lleva a ratios de productividad por operario muy superiores a la media europea, es quizás todo lo referente a la logística lo que diferencia a esta planta. Y es que Volkswagen Navarra ha desarrollado y aplicado un novedoso sistema de logística para la organización de la secuenciación y traslado de las piezas de los vehículos a la línea de Montaje.
El nuevo procedimiento se basa en el empleo de vehículos autónomos y en la digitalización de todo el proceso. Se trata del primer proyecto de estas características aplicado en las fábricas de la marca en Europa, lo que coloca a Volkswagen Navarra a la cabeza de la automatización logística en el conjunto de la compañía. Este proyecto se enmarca en la estrategia de automatización y digitalización de los procesos logísticos puesta en marcha por Volkswagen Navarra hace unos años.
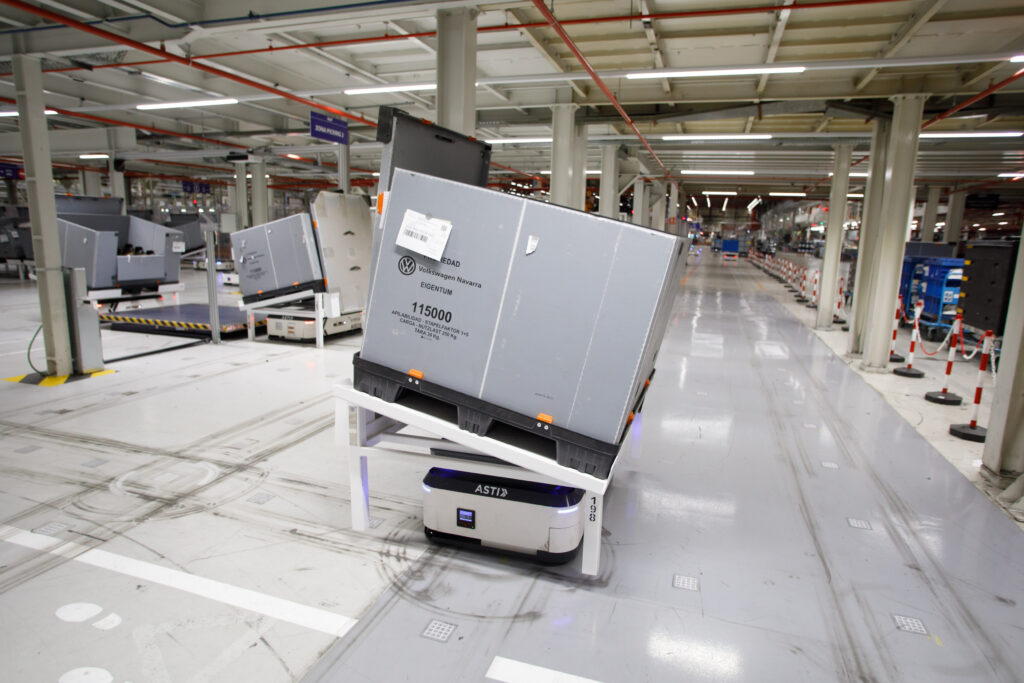
El sistema implementado concierne a la parte del proceso logístico donde se secuencian las piezas de la línea de Montaje para todos los modelos que produce la factoría de Landaben: Polo, T-Cross y Taigo. La principal ventaja aportada por el proyecto, además de la propia automatización, consiste en el mayor aprovechamiento del espacio, lo que contribuye a no tener que recurrir a almacenes externos por la producción del tercer modelo, Taigo. Como consecuencia, Volkswagen Navarra mejora los costes operativos al reducirse los transportes exteriores.
“No se trata tan sólo de un cambio de proceso o de un proceso típico de automatización. Es algo mucho más profundo que ha provocado una transformación radical en la forma de trabajar. Sin duda, supone un paso de gigante hacia la logística autónoma”, señala Alfonso Eslava, director de Logística de Volkswagen Navarra. El proceso comienza por la necesidad de material en el punto de montaje. La petición llega de forma digitalizada a la zona de secuenciación donde un operario secuencia las piezas en el orden que las precisa Montaje colocándolas en carros preparados al efecto.
Una vez finalizado el proceso de secuenciación de cada carro, éstos se suministran mediante vehículos autónomos que a su vez gestionan su retorno cuando están vacíos. Cuando el operario que realiza la secuenciación necesita reponer el material, lanza una petición al almacén, que se tramita de forma paralela al sistema que gestiona esos vehículos, para que estos se encarguen de retirar el contenedor vacío y realicen la reposición del lleno, colocado previamente por un operario en la zona de transferencia.
Al utilizar vehículos autónomos, se reduce de forma significativa el empleo de carretillas, creando un espacio de trabajo con una clara separación entre la zona de circulación de los vehículos autónomos y la zona por donde transitan las carretillas. De este modo, el riesgo de accidentes se reduce notablemente. Todo el proceso está basado en la utilización de diferentes sistemas informáticos interrelacionados, por lo que el trabajo del departamento de Tecnologías de la Información (IT) de la fábrica ha sido fundamental.